|
Products :
Jointing Sheets
|
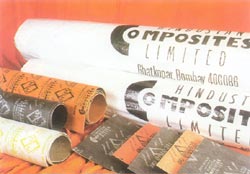
Hindustan composites Ltd. has been in the field of manufacture of
insulating and sealing materials for over 45 years now. Compressed
asbestos fibre jointings developed and manufactured with overseas
technical backup by Hindustan composites Ltd has been more than
satisfying the needs of the industry domestically as well as
overseas.
Compressed asbestos fibre jointings are manufactured from
carefully selected chrysotile fibres, intimately blended with
suitable heat resisting binders, fillers and vulcanised into
sheets of homogenous compositions and uniform thicknesses.
To avoid the necessity of producing perfect finish on the contact
faces of a mechanical assembly, which is not only costly but quite
often impracticable, a gasket from compressed asbestos firbe
jointings enables a tight seal to be created and maintained
between separable members. The seal is effected by the yielding,
or the flow of the jointing material into the imperfections of the
joint contact faces. In this way the gasket provides an unbroken
barrier of homogenous structure through which no pathways exist
for escape of the confined media.
Highly specialized knowledge and technical skill is necessary to
manufacture adequate grades of compressed asbestos fiber jointings
to various service parameters, such as resistance to contained
fluid and pulsating loads if necessary.
The engineers and technicians involved in design, production and
maintenance are quite familiar with the wide range of compressed
asbestos fibre jointings manufactured by Hindustan composites and
hitherto marketed under the brand names of 'permanite' and
'firefly' CAF. These jointings after upgradation, wherever
necessary are now being offered under our export brand name 'FYSAX'.
Our R&D center with its highly specialized and experienced staff
continues to provide all the backup services for upgradation of
technology and products to meet the highest quality and
performance standards while keeping pace with the accelerated rate
of technological advancement and demand for excellence from the
industry.
This catalogue contains the comprehensive data in the from of
guidelines for engineers and technicians to enable them to select
the appropriate grade of jointing materials for application from
the wide range available. However the numerous parameters under
which the jointing is expected to meet manifold demands may make
the selection difficult. Our Technical cell would be most
delighted to help solve your problems promptly.
Choice Of Jointing Grade
|
The choice of the grade of jointing material for any and
given condition is of paramount importance. A number of factors
need to be taken into consideration, while the choice of the
correct grade and thickness is finally made for a particular
application. |
|
Type Of Confined Media
|
Resistance to attack by the confined media on
the jointing material forms the sole basis of selection. Please
refer to the Fibre jointings Recommendation chart given at the
end. Though other factors also play an important role in the
selection procedure these guidelines serve the purpose
adequately. |
|
Flange Surface Finish
|
Too smooth a surface would be detrimental.
The gasket and flange surface must provide suitable friction to
reduce the chances of the gasket bursting under pressure. |
|
Concentric grooves, particularly the standard
gramophone record or spiral type are most ideal, though.
Commercial machine finish would do in most cases. However the
jointing material itself should have a high surface co-efficient
of friction, so that it may be firmly gripped between the flange
faces. This characteristic of the jointing though appears to be
insignificant for consideration, plays an important role in
reducing the possibilities of gasket burst. Hindustan Composites
pays special attention to technology of surface compounds to
meet this requirement. |
|
Gasket and Bolt Configuration
|
For a given gasket stress, the possibilities
of leakages will increase as the width of the gasket decreases.
Placement of bolts to even out the stress is also an important
consideration while designing the flange. |
|
Clamping Pressure
|
Actual initial compression needed on a gasket
to reduce leakage to zero or to an acceptable level, also known
as minimum gasket sealing stress depends upon the following: |
|
-
Design of the flange and bolt configuration
-
Internal pressure of the fluid
-
Viscosity of the contained fluid and its temperature which
has an effect on the viscosity
|
|
Generally the actual clamping pressure is
increased over the minimum gasket sealing stress by multiplying
internal pressure by a factor known as the 'Gasket Factor'. As a
thumb rule, the gasket factor for liquids is 1 and that for
gases is 2.5. |
|
Choice Of Thickness
|
Though there are no hard and fast rules
governing the choice of gasket thickness, the gasket should be
as thin as possible to minimize the stress relaxation. The
considerations are, dimensions and conditions of the flange. As
a guideline the following choices can be made, depending upon
the condition of the flange surface: |
|
FLANGE SURFACE |
Finely ground |
Finely machine finished |
Normally machined |
Rough machined |
Well forged or die-cast |
THICKNESS |
0.25 to 0.4 mm |
0.5 to 1.00 mm |
1.2 to 1.5 mm |
1.5 to 3.0 mm |
3.0 mm and above |
|
|
Important Characteristics Of Jointing Materials
|
Specifications covering the physical
properties basically help in classifying the grades of jointing
materials. For example, in recent years there has been an
increasing tendency to take tensile strength as being the total
measure of the quality and likely performance, but in reality it
is by any means, not the sole criterion to judge its possible
behavior in service. The following characteristics also play an
important role in determining how efficiently the jointing
material performs under varying operating parameters. |
|
-
Compressibility - A jointing material should
possess compressive characteristics so that it allows the
material to flow and conform to the flange surface with an
ability to 'bed-in' and offer necessary friction.
-
Recovery - As the jointing material should get
compressed under pressure, it should also offer resilience to
recover and maintain its sealing effect by not allowing any
'Permanent Set' due to changes in pressure of the confined
fluid and effects of its temperature, or due to flange
deflection or bolt expansion.
-
StressRelaxation - This determines the dimensional
stability of the jointing material under combined effects of
pressure and temperature. There should be a minimum tendency
of the gasket to relax its stresses under high
pressure/temperature conditions to reduce the torque loss and
maintain an effective seal.
|
|
Hindustan Composites Limited strive to
maintain these important characteristics in its jointing
material, through well formulated furnished, controlled
manufacturing process, stringent checks and balances at every
stage. |
|
Guidelines On The Use Of FYSAX AMJ Jointings
|
The FYSAX AMJ series of jointings are
carefully designed to perform excellently under normal fitment.
However, certain preparatory precautions would help in achieving
the best results: |
|
-
The flange faces must be clean and devoid of any
projections, dents, burrs, distortion, etc.
-
The OD, ID and the bolt clearances should be cut with a
sharp cutter to avoid folds and burrs.
-
Ensure that the flange surfaces are fully covered by the
gasket to avoid possible corrosion, with adequate clearance
around bolt holes to avoid folds, bulge or shear during bolt
tightening.
-
Avoid contamination of the gasket with oil, grease,
adhesives, etc.
-
Insert the gasket in between the flanges, slip one bolt
and position the gasket and place other bolts.
-
Lightly tighten in the following order and repeat the
order with full spanner pressure.
|
 |
|
Dimensions
|
Range of
Nominal Thicknesses in mm |
0.25 |
0.4 |
0.5 |
0.75 |
1.0 |
1.2 |
1.5 |
2.0 |
3.0 |
4.0 |
5.0 |
6.0 |
|
|
Sizes
|
|
Quality
Thickness |
Range (mm)
|
Sheet Size(mm) |
|
Length
|
Width |
All(except AMJ545 Ultra Metallic) |
1.5 & above |
1550(±50) x |
1550(±50) |
All (except AMJ 493 ACID and
AMJ545 ultra metallic) |
All |
1850(±50) x |
1250(±50) |
AMJ 493 ACID AND AMJ 545
Ultra-Metallic |
0.6 & above |
1850(±50) x |
1250(±50) |
All |
All |
1500(±50) x |
1500(±50) |
|
|
Note
|
Sheet Sizes of 3200(±50)x3200(±50)
,1500(±50)x4500(±50) ,3200(±50)x 1600(±50) can also be supplied
on mutual consent. |
  |
 |